Past Commissions : # 2 Oak French Armoire
Hi Woodworking enthusiasts,

I am writing a series of posts on previous commissions,
You can see the first here: Batman Plaque
I was asked to make a wardrobe by a very good client of mine.
They wanted something for their spare room.
I have made many pieces for this client over the years and with each piece they can see what I can do.
This has made them more relaxed ,they trust in my judgement, and allow me to be artistic.
My criteria was a wardrobe which had carved panels matching an existing Wardrobe in the room.
The rest was up to me, but after discussing it through with them ( and knowing their taste in furniture) I suggested a French armoire.
I had never made one before and it is not my personal taste but I relished the challenge.
The design
I had to do a lot of free research for this one but it is all part of the learning process.
I started with the overall dimensions. I had worked these out on site.
Then I studied French armoires and tried to establish the essence of one.
It was quite tricky as there are so many different types when you look closely.
I got as much information in as I could and started my design.
The vertical uprights and the top of the plinth were my only datum.
I decided the starting point were the scrolls in the centre of the cornice and the cornice itself.
I drew these out full size and made sure I was happy with them.
This part had to be correct as any imperfections in the curves would ripple through the rest of the wardrobe.
I then designed the plinth. This was to be a solid base for the whole structure to rest on.
Once I hade these I designed the frames and doors.
The frame and sides were to be plain and the door panels were to be carved.
I made a scale drawing and presented it to the client. The client wanted the central doors to be carved only.
In my original design I had hanging space in the centre and shelves either side.
This was changed to shelving through out.
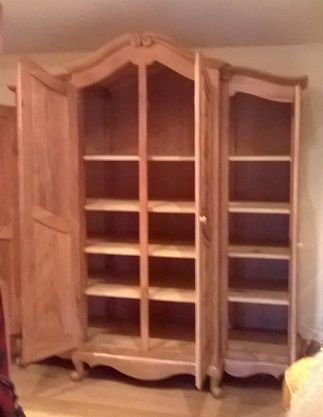
Making the Wardrobe
This was tricky. I had limited straight edges to work to, but the main thing was the focal points.
So as I started the design with the cornice and plinth, I did the same with manufacture.
I made templates out of 1/4" mdf.
Which I transferred on to the oak, choosing the grain carefully.
Because of the complex shapes I did most of this by hand.
Once these were completed I could make the carcase.
Thing got easier for then on.
When the carcase was made I took templates for the doors.
The Doors
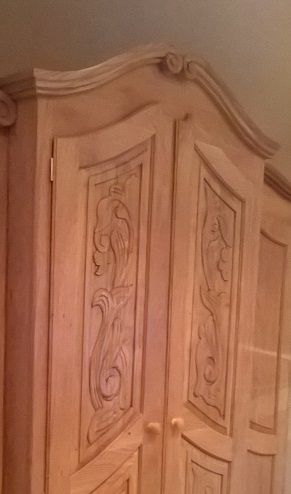
I made the door frames and jointed them mainly by had because of the awkward shapes.
They were mortise and tenoned with a groove for the carved panels.
The panel design had to be elongated from the original .
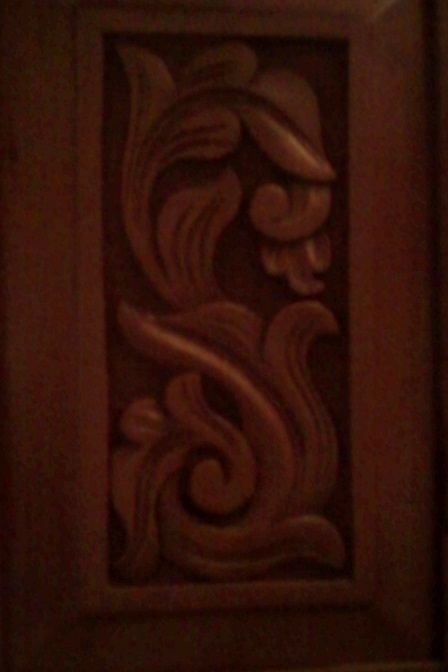
Not only that it had to be a diamond shape so I had to draw it out free hand.
I roughed out the panels with my router and then copied the carving style of the original.
Did I mention that this was December 2016 and the dead line was the 19th.
Every year I plan my work on the run up to xmas months in advance.
That year everything went wrong.
All the jobs I had lined up were postponed or cancelled and totally out of my control.
It was a choice between a very lean Christmas or investing in materials etc and going for it.
I went for it but it was gruelling.
Working through the night and doing two hour sleeping patterns was the norm.
This was so I could wake up and glue up!
I had no choice to succeed. The 19th was the last day until the new year.
All good fun.
The Delivery
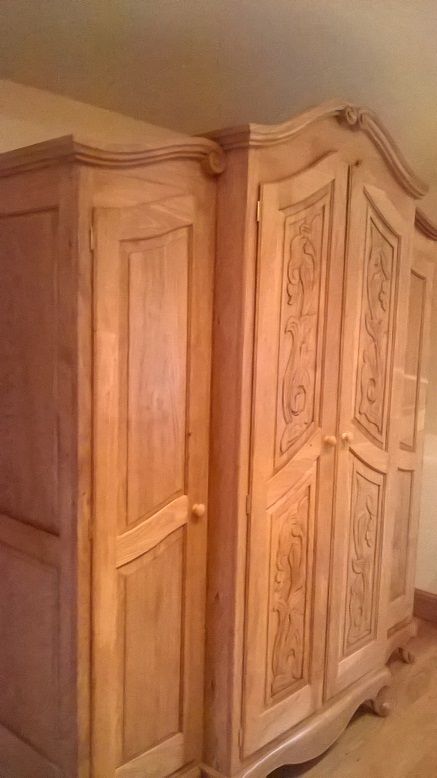
I had designed the wardrobe to be flat pact so that it would fit in through the clients door and be manageable.
I always go over the top on strength and assume the piece will be disassembled and re assembled many times.
I enlisted some help with the carrying and construction.
To be fair it went together well.
The doors were a bit tricky to hang, but have not need adjusting yet.
Did I mention that this was December 2016 and the deadline was the 19th.
I always plan my work up to Christmas months in advance but this year every job was either cancelled or postponed.
I had the choice of a very lean Christmas or going for it.
I went for it.
I had to work through the nights but it was done.
It was a good Christmas that year.
If you have any questions about woodwork, furniture or being self employed as a craftsperson let me know.
I know my wood and I have spent years teaching myself furniture making , furniture history as well as living it as a self employed cabinet maker .
I am also in the process of writing a
'How to series: Setting up a Woodworking Business'
Which you can read here;
Part 1: Workshop
Part 2: Tools and machinery
Part 3: Finding a good timber yard
Part 4: Deciding what type of woodwork you are going to do.
Still I am learning every day and the journey is the point.
Many thanks for reading,
Until next time,
@jist
I mean … wow! That is STUNNING. Seriously, kudos to your skills. What an amazing piece and heirloom they now have.
Woodcarving: I also did a course on this years back. My woodcarving instructor would've cut our hands off if we admitted using a router. He's very pure, old school. That's beautiful carving though.
I'm gonna really enjoy your blogs. Thanks for sharing.
Thank you. I only used the router freehand to take some of the waste away. Just saves time. Thanks for reading.
Yes, that makes sense. Speeds things up a bit. :)
This post has received gratitude of 0.54 % from @appreciator thanks to: @jist.
Beautiful work! resteemed
Thanks mate.
Simply awesome, resteemed
Thanks man
I love the panel designs and it's details. It must be quite challenging to carve? Not sure if it's the correct term. Great job @jist.
Thanks @dawnsheree. Yes that is the correct term and yes they were a bit tricky. The hardest part was setting out the longer design. If that is wrong then everything else is a waste of time.
Yes, I know one wrong move and it's going to be a waste of all your time.
This post has received a 2.77 % upvote from @aksdwi thanks to: @jist.
This post has received a 0.86 % upvote from @boomerang thanks to: @jist
That is what I call serious skill.
It looks fucking majestic.
Especially with the panels.
I imagine a huge working table out of wood just like the one of the president with runes and norse gods carved in them.
I would pay 1000USD for such a table.
Thank you. I spent ages getting the proportions and the design right. It is an honour to make pieces like that. When clients let me do my thing they get a lot for their money because it put my all into it. Literally bold, sweat and almost tears.
That is the resolute desk in the white house. It was a gift from queen Victoria and it was made from oak from a ship called the HMS Resolute. That would have been some serious oak from back in the day.
The Vikings had a really cool carving style I really like the boat carvings.
Fuck, I will probably order one and have it delivered from the states (I don't care about the massive delivery costs) and pay around 5K for it, you better get some practice.
I want a presidents table with runes and Norse gods carved into it in the future.
I like that top one of Thor.
You got a 39.73% upvote from @upyou thanks to @jist!
1.48% @pushup from @jist