Producción de aluminio
Quiero hablarles desde el punto de vista de la producción del aluminio como ingeniero, independientemente de su especialidad, deben adquirir conocimientos básicos y aplicaciones sobre los procesos y nuevas tecnologías aplicada en este campo. Recordando que los materiales se pueden agrupar dentro de cinco categorías: Metálicos, Poliméricos, Cerámicos, Compuestos y Electrónicos.
El aluminio posee características que hacen ser uno de los mejores materiales utilizados en el mundo, para mas información le recomiendo leer un post que le dedique completamente a el aluminio.
Materia Prima
Producción
El aluminio es el elemento metálico más abundante en la corteza terrestre y siempre se presenta combinado con otros elementos como hierro, oxígeno y silicio. La bauxita, que consiste principalmente en óxidos hidratados de aluminio, es la materia prima más utilizada para la producción de aluminio. En el proceso Bayer, la bauxita reacciona con hidróxido sódico. Después de la separación del material insoluble se precipita el hidróxido de aluminio de la disolución de aluminato. El hidróxido de aluminio es luego espesado y calcinado a oxido de aluminio Al2O3.
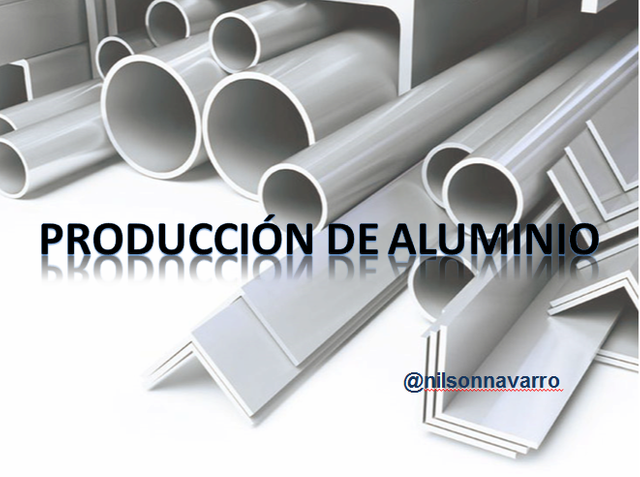
El óxido de aluminio se disuelve en un baño fundido de criolita ( Na3AlF6) y se electroliza en una celda electrolítica utilizando ánodos y cátodos de carbono. El la electrolisis se obtiene el aluminio metálico en estado líquido que cae al fondo de la celda y se extrae periódicamente. Este aluminio extraído de la celda contiene entre un 99,5 y un 99,9 por 100 de aluminio, siendo las principales impurezas hierro y silicio.
El aluminio de la celda electrolítica se lleva a grandes hornos revestidos de material refractario donde se afina antes de la colada. Los elementos de la reacción individualmente o en forma de lingotes que lo contenga, pueden fundirse también y ser mezclados con la carga en el horno. En la operación de afino, el metal liquido normalmente se pulga con cloro gas para separar el hidrogeno disuelto, después se des espuma para separar el metal oxidado de la superficie del metal líquido. Después de que el metal ha sido des gasificado y des espumado, se clasifica y cuela en lingotes para refusión o como lingotes primarios para láminas o lingotes de extrusión para posterior fabricación.
Aleaciones de Aluminio
- Aleaciones de aluminio para forja
Para su fabricación los lingotes para chapa o para extrusión se moldean generalmente de modo semi-continuo por el método de enfriamiento directo. En el caso de planchones (lingotes de sección rectangular), se separa el metal de la superficie del lingote que va a entrar en contacto con los rodillos del laminado en caliente. Esta operación se le llama descostrado y se realiza para asegurar la limpieza y tersura de la superficie de las chapas o placas a fabricar, estos lingotes se precalientan u homogenizan a altas temperaturas por un periodo aproximado de 10 a 24 horas para permitir que la difusión atómica consiga una composición uniforme del lingote.
El precalentamiento debe realizarse a una temperatura de fusión más baja. Para identificar las aleaciones de aluminio para forjar se utilizan una designación numérica de 4 dígitos. El primer digito indica el grupo de aleaciones que contienen elementos de aleación específicos. Los dos últimos dígitos identifican la aleación de aluminio o indican la pureza en aluminio. El segundo digito indica la modificación de la aleación original o los límites de impureza.
- Aleaciones de aluminio para forja no tratables térmicamente
Estas aleaciones no pueden ser endurecidas por precipitación y tan solo el trabajo en frio puede incrementar su resistencia. Los tres principales grupos de aleaciones de aluminio para forja no tratables térmicamente son los grupos 1xxx, 3xxx, 5xxx.
Aleación 1xxx: Estas aleaciones tienen un mínimo de 99,o% de aluminio con hierro y silicio como impurezas mayoritarias.
Aleación 3xxx: El manganeso es el principal elemento de aleación de este grupo y la resistencia del aluminio se consigue principalmente por endurecimiento por disolución sólida.
Aleaciones 5xxx: El magnesio es el principal elemento de aleación de este grupo y se añade para endurecer por disolución solida hasta cantidades superiores al 5%.
- Aleaciones de aluminio para forja tratables térmicamente
Algunas aleaciones de aluminio pueden ser tratadas térmicamente para endurecerlas por precipitación. Los grupos de aleaciones de aluminio para forja tratables térmicamente son 2xxx, 6xxx y 7xxx son todas endurecibles por precipitación.
Aleaciones 2xxx: El principal elemento de aleación de este grupo es el cobre, pero en la mayor parte de estas aleaciones puede añadirse también magnesio.
Aleación 6xxx: Los principales elementos de aleación para este grupo son el magnesio y el silicio, que combinados entre ellos forman un compuesto intermetalico Mg2Si, que en forma de precipitado endurece este grupo de aleaciones.
Aleaciones 7xxx: Los principales elementos de aleación para el grupo 7xxx de aleaciones de aluminio son cinc, magnesio y cobre. El cinc y el magnesio se combinan para formar un compuesto intermetalico, MgZn2, que es el precipitado principal que endurece estas aleaciones cuando se tratan térmicamente.
- Aleaciones de aluminio para Fundición
Las aleaciones de aluminio normalmente se moldean mediante tres procesos: fundición en arena, fundición en molde permanente y fundición en coquilla.
Fundición en arena: Es el más sencillo y el más versátil de los procesos de fundición de aluminio. Este proceso se escoge para pequeñas cantidades de pieza moldeadas idénticas, para piezas moldeadas complejas con núcleos complicados o piezas moldeadas grandes o estructurales.
Fundición con molde permanente: El metal líquido se vierte en el molde por gravedad, al vacío, o solamente por presión centrifuga. Estas piezas poseen por lo general menores contracciones y menor porosidad que las moldeadas en arena pero, estos moldes permanentes tienen una limitación en tamaño y las piezas con partes complejas pueden presentar dificultades o ser imposibles de obtener por moldes permanentes.
Fundición de coquilla: Se moldean piezas idénticas a la máxima velocidad de producción forzando el metal fundido a entrar en los moldes metálicos bajo presiones considerables. Las dos partes de la matriz metálica se engatillan de forma segura para resistir presiones elevadas. El aluminio fundido se obliga a repartirse por el interior de la cavidad de la matriz. Cuando el metal ha solidificado, las matrices se desbloquean y se abren para extraer la pieza moldeada caliente.
Algunas ventajas de la fundición a presión es que las piezas obtenidas están casi totalmente acabadas y puede producirse a elevadas velocidad, aparte la tolerancias dimensionales de cada pieza fundida pueden mantener más minuciosamente controladas que en cualquier otro de los principales procesos de fundición. Otra ventaja es que se obtienen superficies lisas, el enfriamiento rápido produce estructuras de grano fino y el proceso se puede automatizar.
- Composición de las aleaciones de aluminio para fundición
Las aleaciones de aluminio para fundición se han desarrollado para que tengan cualidades de colada como fluidez y fácil alimentación, así como buenas propiedades como resistencia, ductilidad y resistencia a la corrosión. Como resultado de ello, sus composiciones químicas difieren mucho de las aleaciones de aluminio para forja.
El silicio en el intervalo entre 5 y 12% es el elemento de aleación más importante en las aleaciones de aluminio para fundición puesto que aumenta la fluidez del metal fundido y su facilidad para alimentar el molde, así como el refuerzo de aluminio. La adición de magnesio en un intervalo entre 0,3 y 1% da lugar a un aumento de la resistencia, principalmente por endurecimiento por precipitación mediante calentamiento térmico. El cobre en un rango de 1 y 4% se añade a veces a algunas aleaciones de aluminio para fundición para aumentar la resistencia, particularmente a temperaturas elevadas. Otros elementos de aleación como el cinc, estaño, titanio y como pueden incorporarse a algunas aleaciones de aluminio para fundición.
En algunos casos si la velocidad de enfriamiento de la pieza en el molde es suficientemente rápida, se puede obtener una aleación tratable térmicamente en condiciones de sobresaturación. De este modo, las etapas de tratamiento térmico de solubilización y temple pueden ser omitidas en el proceso de endurecimiento por precipitación de la fundición y solo se requiere la subsiguiente maduración de la pieza una vez se ha retirado el molde.
Procesos de Producción en el Mundo
El aluminio es uno de los elementos más abundantes de la corteza terrestre (8 %) y uno de los metales más caros en obtener. La producción anual se cifra en unos 33,1 millones de toneladas, siendo China y Rusia los productores más destacados, con 8,7 y 3,7 millones respectivamente. Una parte muy importante de la producción mundial es producto del reciclaje. En 2005 suponía aproximadamente un 20 % de la producción total. A continuación se lista unas cifras de producción:
La materia prima a partir de la cual se extrae el aluminio es la bauxita, que recibe su nombre de la localidad francesa de Les Baux, donde fue extraída por primera vez. Actualmente los principales yacimientos se encuentran en el Caribe, Australia, Brasil y África porque la bauxita extraída allí se disgrega con más facilidad. Es un mineral rico en aluminio, entre un 20 % y un 30 % en masa, frente al 10 % o 20 % de los silicatos alumínicos existentes en arcillas y carbones. Es un aglomerado de diversos compuestos que contiene caolinita, cuarzo óxidos de hierro y Titania, y donde el aluminio se presenta en varias formas hidróxidos como la gibbsita Al (OH)3, la bohemita AlOOH y el diásporo AlOOH.
La obtención del aluminio se realiza en dos fases: la extracción de la alúmina a partir de la bauxita (proceso Bayer) y la extracción del aluminio a partir de esta última mediante electrolisis. Cuatro toneladas de bauxita producen dos toneladas de alúmina y, finalmente, una de aluminio. El proceso Bayer comienza con el triturado de la bauxita y su lavado con una solución caliente de hidróxido de sodio a alta presión y temperatura. La sosa disuelve los compuestos del aluminio, que al encontrarse en un medio fuertemente básico, se hidratan:
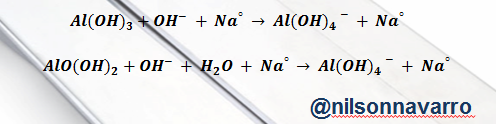
Los materiales no alumínicos se separan por decantación. La solución cáustica del aluminio se enfría luego para recristalizar el hidróxido y separarlo de la sosa, que se recupera para su ulterior uso. Finalmente, se calcina el hidróxido de aluminio a temperaturas cercanas a 1000 °C, para formar la alúmina.
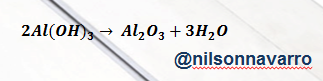
El óxido de aluminio así obtenido tiene un punto de fusión muy alto (2000 °C) que hace imposible someterlo a un proceso de electrolisis. Para salvar este escollo se disuelve en un baño de criolita, obteniendo una mezcla eutéctica con un punto de fusión de 900 °C. A continuación se procede a la electrólisis, que se realiza sumergiendo en la cuba unos electrodos de carbono (tanto el ánodo como el cátodo), dispuestos en horizontal. Cada tonelada de aluminio requiere entre 17 y 20 MWh de energía para su obtención, y consume en el proceso 460 kg de carbono, lo que supone entre un 25 % y un 30 % del precio final del producto, convirtiendo al aluminio en uno de los metales más caros de obtener. De hecho, se están buscando procesos alternativos menos costosos que el proceso electrolítico.
El aluminio obtenido tiene un pureza del 99,5 % al 99,9 %, siendo las impurezas de hierro y silicio principalmente. De las cubas pasa al horno donde es purificado mediante la adición de un fundente o se alea con otros metales con objeto de obtener materiales con propiedades específicas. Después se vierte en moldes o se hacen lingotes o chapas.
Técnicas de procesado
El mineral del que se extrae el aluminio casi exclusivamente se llama bauxita. Una vez obtenida la bauxita, se refina y reduce mediante lavados hasta lograr polvo de alúmina. El proceso de fundición comienza con una técnica llamada Hall-Héroult, en la cual la alúmina (Al2O3) es disuelta dentro de una cuba con criolita mineral fundida (Na3AlF6), revestida interiormente de carbón en un baño electrolítico.
La alúmina se descompone en aluminio y oxígeno molecular. Como el aluminio líquido es más denso que la criolita se deposita en el fondo de la cuba, de forma que queda protegido de la oxidación a altas temperaturas. El oxígeno se deposita sobre los electrodos de carbón, quemándose y produciendo el CO2. El aluminio fundido se enfría en moldes para dales forma de lingote y se vende a los fabricantes con esta forma, sin embargo Son necesarios más de 2.000 °C para fundir el aluminio recién producido, por lo que Hoy en día, la receta se adapta a la aplicación final; Con la ayuda de aditivos (magnesio, silicio, manganeso, etc.), se preparan distintas aleaciones que posteriormente conforman las propiedades mecánicas. Por lo tanto, las posibilidades de procesado del cliente pueden establecerse en una fase muy temprana.
Otra forma de presentar el aluminio en el mercado es en forma de tochos de extrusión, esto es una especie de barra gruesa de material puro que tiene la forma precisa para introducirse en una prensa de extrusión. Esta técnica es muy común, debido a la gran gama comercial del aluminio en perfiles para ventanas, puertas corredizas, etc. La extrusión consiste en hacer pasar un tocho de aluminio precalentado (450-500ºC) a alta presión (1600-6500) toneladas, dependiendo del tamaño de la prensa) a través de una matriz, cuya abertura corresponde al perfil transversal de la extrusión.
Nuevas Tecnologías
El Aluminio transparente Desarrollado por el US Naval Research Naval, es magnesio aluminado fabricado en planchas, y que destaca por una resistencia muy superior a las aleaciones actuales. El nombre que tiene no es sino porque, evidentemente, es transparente, y otros datos interesantes tienen que ver con que es muy maleable, luego se pueden crear todo tipo de formas con él.
El Instituto Tecnológico de la Energía (ITE), junto con JAP Energéticas Medioambientales SL e INDETEC, concluyó el desarrollo de una nueva tecnología con la que se busca, a partir de residuos industriales de aluminio y amoníaco, obtener hidrógeno para alimentar una pila de combustible que genere energía. El objetivo principal de este proyecto, es conseguir hidrógeno a partir de dichos residuos industriales, con un proceso basado en la reón entre aluminio y agua. El hidrógeno producido alimentará una pila de combustible, que generará energía para ser utilizada en diversos fines, informa en un comunicado el ITE, con sede en Valencia. El uso de hidrógeno es una alternativa viable, rentable y limpia con expectativas de futuro, y puede suponer un punto de inflexión en el uso de energías tal como está concebido actualmente, indican las mismas fuentes.
Bibliografía
ASQUELAND, Donald R y Phule Pradeep P. Ciencia e Ingeniería de los Materiales. Editorial: International Thomson Editores S.A. México (2006).
SMITH, William. Ciencia e Ingeniería de los Materiales. 3era Edicion. Editorial Mc Graw Hill. Mexico (2004).
Congratulations! This post has been upvoted from the communal account, @minnowsupport, by nilsonnavarro from the Minnow Support Project. It's a witness project run by aggroed, ausbitbank, teamsteem, theprophet0, someguy123, neoxian, followbtcnews, and netuoso. The goal is to help Steemit grow by supporting Minnows. Please find us at the Peace, Abundance, and Liberty Network (PALnet) Discord Channel. It's a completely public and open space to all members of the Steemit community who voluntarily choose to be there.
If you would like to delegate to the Minnow Support Project you can do so by clicking on the following links: 50SP, 100SP, 250SP, 500SP, 1000SP, 5000SP.
Be sure to leave at least 50SP undelegated on your account.