The Effects of Silicon on Steels
There are lots of elements can be found on our planet, but let’s focus one of this which plays many roles in the production of steels. I’m referring to elements of silicon.
Our planet has about quarter of silicon. It is mined as quartz, sand, mica, feldspars, talc, vermiculite, and others. Silicon has atomic number 14 and has a symbol of Si. Yes! It is a chemical element. It is hard and brittle crystalline solid having a metallic luster which is blue-grey. Silicon is a semiconductor and a tetravalent metalloid. It is also unreactive compared to germanium and has a high affinity for oxygen. It has this ability to remove oxygen that makes silicon important in the production of steel.Removal of Oxygen
Aside from aluminum, ferrosilicon, and manganese, silicon has a significant role in deoxidizing steels, that’s why it is called ‘’Killed Steel’’. The so-called killed steel are those steel that has dioxide completely through the addition of agent before casting. Meaning, no presence of gas evolution during solidification. Besides, killed steel is said to be ‘’killed’’ because it solidifies in the mold without bubbles coming out.
Talking about killed steels, semi-killed steels usually contain up to 0.10% max silicon, and about up to 0.60% maximum for entirely killed steels. Besides, SAE carbon and alloy steels contain 0.5 – 0.35% amount of silicon.
Influences of Silicon in Different Ways
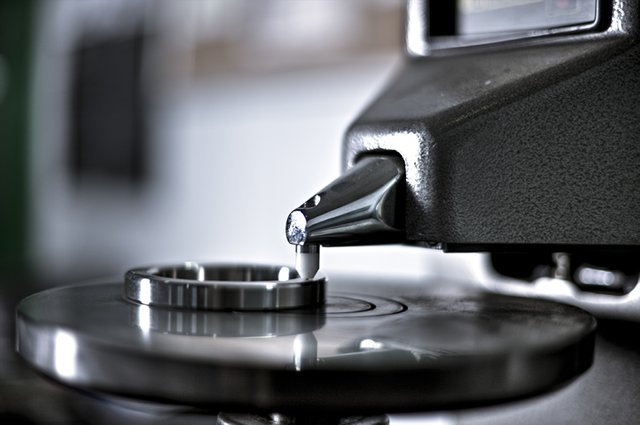
There is a lot of influences silicon can give on steel material. One of this is the increase in hardness and strength. It helps the material to be free from defects, decays, and damages by improving the soundness.
Steel having 0.04% amount of silicon extent affect the appearance and thickness of the galvanized coating. This provides much corrosion protection like a shiny galvanized coating where the outside layer is pure zinc. It also results in a thick coat mainly consisting zinc-iron alloys.
Silicon also has an influence in welding, when carbon content is high, it aggravates cracking, then tendencies. It is also detrimental to surface quality mainly in low carbon, resulphurized grades.Silicon content should not exceed 0.10% to have the best welding condition, but amount up to 0.30% is not severe like phosphorous or sulfur content. That’s it! It is the main reason why silicon is always present in all steels. I hope you learned something today.
Thank you for Reading !
You can also read my previous articles:
- Is Planer and Shaper Machines are Different or Similar?
- Alloy Formation, Methods of Production, And Its Various Applications
- An Overview of Jewelries Manufacturing Processes and Methods
- Plywood Manufacturing Process, Categorization, and its Application
- Why Stainless steel doesn't Corrode Compared to other Steels
- Bicycles An Alternative Source of Energy to Charge Mobile Phones
References:
https://en.m.wikipedia.org/wiki/Silicon
https://en.m.wikipedia.org/wiki/Deoxidized_steel
https://www.corrosionpedia.com/definition/1584/killed-steel
https://pmpaspeakingofprecision.com/2010/10/19/silicon-the-great-influencer-in-your-steel-and-in-your-machine-shop/amp/
https://www.leonghuat.com/articles/elements.htm
wow..
its a great post.
keep it up
wow very important post....