Reducing Downtime in Roadheaders with Advanced Mobile Hydraulic Solutions
In mining, tunneling, and large-scale construction, roadheaders are indispensable machines that help cut through rock and soil to create tunnels, shafts, and spaces for infrastructure. These complex machines operate in demanding environments where high efficiency is critical. However, roadheaders are also susceptible to breakdowns and downtime, disrupting operations and leading to costly delays. The key to minimizing these disruptions lies in advanced mobile hydraulic solutions that enhance performance and reduce the risk of mechanical failure.
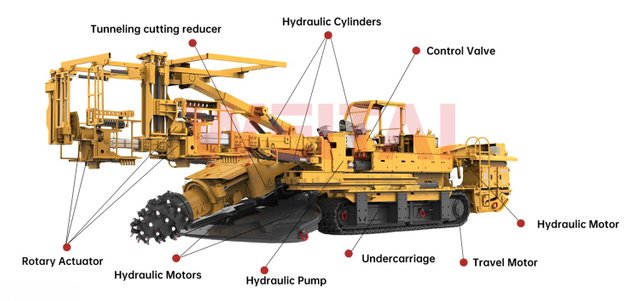
This blog post explores how modern hydraulic technologies reduce downtime in roadheaders, ensuring smoother operations, better reliability, and more cost-effective project outcomes.
The Cost of Downtime in Roadheaders
When a road header breaks down, the financial impact can be substantial. Mining and construction projects often operate on tight timelines, and an out-of-service road header can halt progress entirely. Beyond direct repair costs, downtime also leads to delays in project completion, missed deadlines, and increased labor costs as crews remain idle. Minimizing these interruptions is crucial, and this is where mobile hydraulic solutions come into play.
How Advanced Hydraulic Systems Reduce Downtime
Improved Reliability with Predictive Maintenance
One of the most significant advances in modern hydraulic systems is the ability to monitor machine health in real-time. Advanced sensors embedded in hydraulic components continuously gather pressure, temperature, and flow rate data. This data is analyzed to predict potential failures before they happen.
For example, if a hydraulic pump shows signs of wear, the system can alert the operator to perform maintenance before a complete failure occurs. By scheduling repairs during planned downtime, operators can avoid sudden breakdowns, reducing the likelihood of costly disruptions.
Durable, High-Performance Components
Advanced mobile hydraulic systems use components designed to withstand the rigors of underground work. High-strength materials, specialized coatings, and enhanced sealing technologies ensure that pumps, valves, actuators, and cylinders last longer and operate more reliably.
For roadheaders operating in abrasive environments, such as hard rock or high-dust conditions, components that resist wear and tear are critical. Durable hydraulic systems reduce the frequency of repairs and part replacements, keeping the machine in service for longer periods.
Variable Displacement Pumps for Energy Efficiency
Variable displacement pumps are game-changers for road header hydraulics. Unlike fixed displacement pumps, which operate at a constant flow, variable displacement pumps adjust their output to meet the system's demands. This ensures that the road header uses only the power it needs, reducing unnecessary strain on the hydraulic system.
By reducing the workload on hydraulic components, variable displacement pumps decrease the risk of overheating and mechanical failure, contributing to fewer breakdowns and longer machine uptime.
Hydraulic Fluid Filtration Systems
Contaminated hydraulic fluid is one of the leading causes of system failure. Dirt, metal particles, and debris can enter the hydraulic system, causing wear and damage to pumps, valves, and actuators. Advanced mobile hydraulic solutions include sophisticated filtration systems that keep the fluid clean, extending the life of components.
Conclusion
These systems often feature self-cleaning filters that automatically remove contaminants from the fluid, reducing the need for manual cleaning and ensuring that the hydraulic system operates at peak performance.