Petroleum Engineering: Drill String Design

Image source
The drill string is a set of pipes in charge of fulfilling a specific function, these pipes are the ones that rotate and with the weight that the whole string has, they drill the rock in the subsoil, as the drilling of the well goes deeper, more pipes are added to the set of drill pipe string.
It is important to highlight that the drilling fluid (drilling mud) circulates inside the pipes that make up the drill string, it comes out through the small holes that the drill bit has, the drill bit which is the component that cuts the rock in the subsoil is also assembled to the drill string, if the drill string rotates, then the drill bit rotates and with its teeth cuts the rock in the subsoil.
In engineering terms, it is important to take into account that if the drill string rotates, then the bit rotates and with the resistance that forms the rock in the subsoil to be cut a torque or moment is generated, if this torque or moment exceeds the values allowed to yield or break the pipe, then the pipe string may collapse, as shown in the following image:

Image source
What does the drill string consist of?
If we take into account the order of the components from the bottom to the top, the drill string is first composed of the drill bit, which is this element that I show below:
The bit shown is a triconical bit, which according to its rock cutting mechanisms at the bottom is widely used for drilling in the first 1000 feet of depth, where the rocks still do not show much hardness, and when it is necessary to use a bit to cut harder rocks at the bottom, PDC bits are used:
The design that the drilling engineer executes in the use of these bits will depend to a great extent on the degree of resistance to cutting that the rock presents in the subsoil, the variability in the hardness of the rock also has to do with the depth to which it is intended to reach in the drilling of the well, since the deeper the rock is, the harder it is. It is important that the design in the use of the drill bits is as optimal as possible, since otherwise, the drilling costs of the oil well would increase.
After the drill bit comes the bottom hole assembly (BHA), the BHA is basically formed by the drill bit, which is a component that has already been explained, and is formed by tubes called drill chucks, which are basically heavy drill pipes that will give the weight to the drill bit so that it can cut the rock at the bottom when the string rotates. The drill collars are also called drill collars, besides giving weight to the bit they also provide rigidity to the drill string, here is a picture of the drill collars:
Above the drill collars, some stabilizers are placed, which will allow the drill string as a whole to remain stable, here is a picture of a stabilizer:

Image source
The named components would be the components of a basic BHA, meaning that there may be other components that make up a BHA, that will depend on the section of the well to be drilled, for example if you are going to drill the section of the first 1000 feet deep (conductive hole) is very applicable this type of BHA, however if we are drilling the intermediate hole at a depth that can be in the range of 5000 feet to 12000 feet, then the BHA must have a downhole motor, which allows the drill bit to rotate without the need to rotate the string, here is the image of a downhole motor:
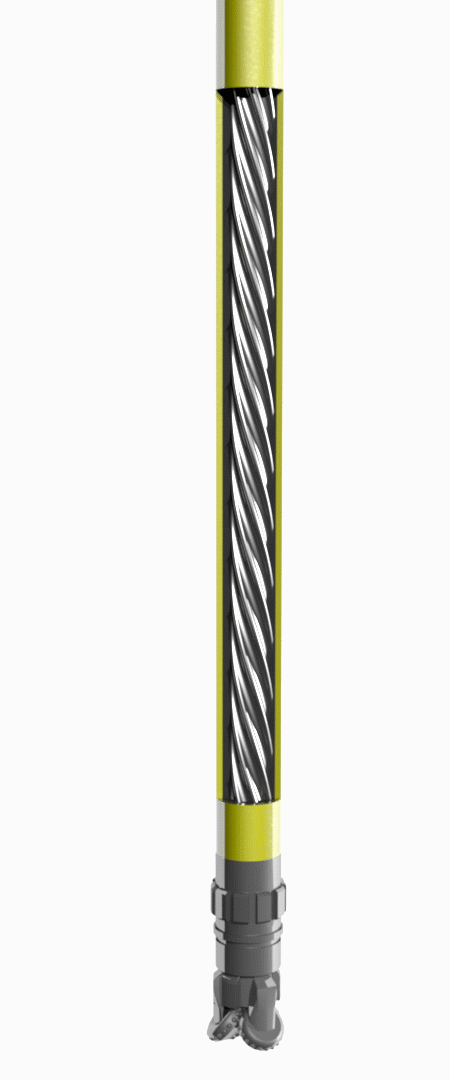
Image source
At the depth of the intermediate hole, many times by design it is necessary to deviate the trajectory of the well, so it is convenient that the BHA has a directional rotary system, since with this system we can build a directional well with the desired angle and direction. If we want to take advantage to measure some parameters at that depth, then we would have to add to the BHA measurement and logging tools while drilling.
If the diameters of these components are not the same, there is no problem, as they are screwed into the drillstring using connectors of different rocks and diameters.
As the drill string should not be so rigid, a type of pipe is needed that is heavy but has flexibility, for this a type of pipe called transition pipe is used, also called heavy drill pipe, the amount of heavy drill pipe will depend on the design considered by the drilling engineer taking into account the depth of the well and the type of rock in the subsoil that has to be cut.
The advantage of this type of pipe is that it provides a more flexible string but still provides weight to the drill bit.
Above the heavy drill pipe is placed the drill pipe, the drill pipe is the largest amount of pipe added to the drillstring, because as drill pipe is added is because it continues to deepen the drilling of the oil well.
Below is a picture of the drill pipe:

Image source
Drill string design must consider multiple variables, ranging from the stresses that the string will be subjected to downhole as the oil well is being drilled, to the amount and type of pipe and tools that will be placed in the drillstring.
Poor drillstring design can cause high torque to cause the drillstring to break downhole, delaying operations and increasing drilling costs.
Recommended references
Morris, William, "Manner of uniting augers to sinkers for boring artesian wells", published 4 September 1841.
Guillod, Edward, "Improvement in the construction of drilling-jars", published 16 June 1868, assigned to Bryan Dillingham & Co.
Bodine Jr., Albert G., "Acoustic method and apparatus for moving objects held tight within a surrounding medium", published 21 February 1961.
O. Gonzalez, "Retrieving Stuck Liners, Tubing, Casing And Drillpipe With Vibratory Resonant Techniques" Society of Petroleum Engineers Paper # 14759.
O. Gonzalez, Henry Bernat, Paul Moore, "The Extraction of Mud Stuck Tubing Using Vibratory Resonant Techniques" Society of Petroleum Engineers Paper # 109530.